Hydraulic Brake - Anti-lock System 4
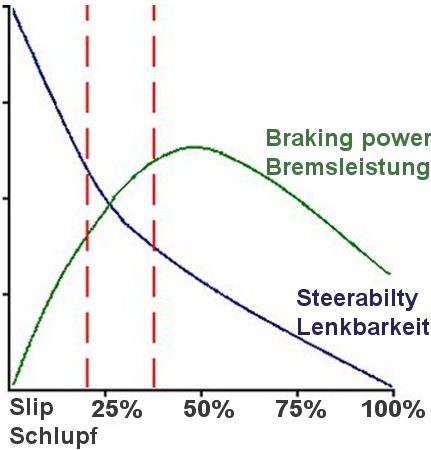
Clearly here is proof that ABS is not looking for the shortest stopping distance. That would be 50 percent slippage. But now we have to clarify what slippage is. It arises as the difference of the distance traveled in a freely
rolling and a either accelerated or decelerated wheel.
If we assume, for example, the tire size 205/55 R 16, then the inner diameter of the rim 16'' * 25.4, so 40.64 cm in size. In addition there are 2 * 20.5 cm * 0.55, so 22.55 cm for the tire above and below the rim. A wheel
with a diameter of 63 cm thus has a circumference of almost 2 m. Leaving aside the sinking of the wheel mounted on the vehicle, one turn of the wheel would have to lead to 2 m.
If the wheel returns less in one turn, it will spin because it accelerates. If the distance covered is longer then this happens during braking. The percentage of the passed difference to the distance itself is the slip. With
50 percent slippage, the wheel turns as little as for 25 meters over a distance of 50 meters.
And amazingly, that would be the slip that an ABS system would have to aim for to get the best stopping distance. But it does not, as the diagram above shows. The slip ranges between 20 and 35 percent. And that's
because of the steering ability, which is still fairly well preserved in this area. Some braking distance is sacrificed so as not to endanger it.

1 | Driving speed |
2 | Wheel acceleration |
3 | Wheel slip |
4 | Inlet valve |
5 | Outlet valve |
6 | Braking pressure |
And now it's time to take a closer look at the control cycles, because the control processes are in time a little bit different from the parameters previously described. So we go to the question, which value changes how at
which time. For this we first look at the brake pedal. It is clearly most important that is for the whole process.
ABS operations can in principle only be triggered during braking. So if, for example, when searching for errors in the system, such occur in sharp turns without brake actuation, they are to be assigned to ESP and not to
ABS.
So let's operate the brake pedal and reduce the driving speed 1. The acceleration 2 of the wheel considered here is negative, but not very much. Slight wheel slip 3 is always present through the tire. It now takes higher
values. Incidentally, braking without it is inconceivable.
In order for us to get into an ABS regulation, the intensity of the braking process must be increased. The circumferential acceleration is significantly negative, the driving speed decreases faster. At the same time, the
slip reaches a first critical value. This triggers warning level 1 on the control unit. It closes the valve in the line coming from the master cylinder (input valve 4).
It is not enough, the driving speed decreases more, the negative acceleration (delay 2), as well as the brake slip. The control unit reacts with opening of the return valve 5, the brake pressure 6 decreases. But at
first, the measures are not yet effective. It takes a moment to stop the negative trend at the driving speed, so the acceleration 2 will be zero.
Finally the slip has exceeded its highest value. It is now drastically decreasing at the wheel with the brake released. The wheel accelerates violently on the peripheral speed of the other wheels. In the maximum of the
acceleration in this diagram, the value for the brake slip has fallen so far that the connection to the master cylinder 4 can be opened again.
As the valve to the return line had been closed long before. A pressure sensor signals the controller a successful pressure decrease. Somehow, the return pump had to be put into operation. However, if the driver
remains at full braking on the brake pedal, the whole cycle starts again. Time between openings eg of valve 5: estimated 100 milliseconds.
|